A GMP Compliant Packaging Supplier
Dana Poly is a GMP compliant packaging supplier that specializes in GMP certified manufacturing and food packaging. Get an array of different products and packaging supplies from Dana Poly that are GMP compliant. Reach out to us today for more information.
When you reach out, we can provide you with a quote for the plastics you need. Get GMP compliant packaging at affordable prices when you turn to Dana Poly! This packaging can be for food, as well as for the pharmaceutical industry (GMP Certified Pharmaceutical Packaging). We also make customization simple and easy. Learn more about our FDA approved plastic bags and how they will make your company more reliable.
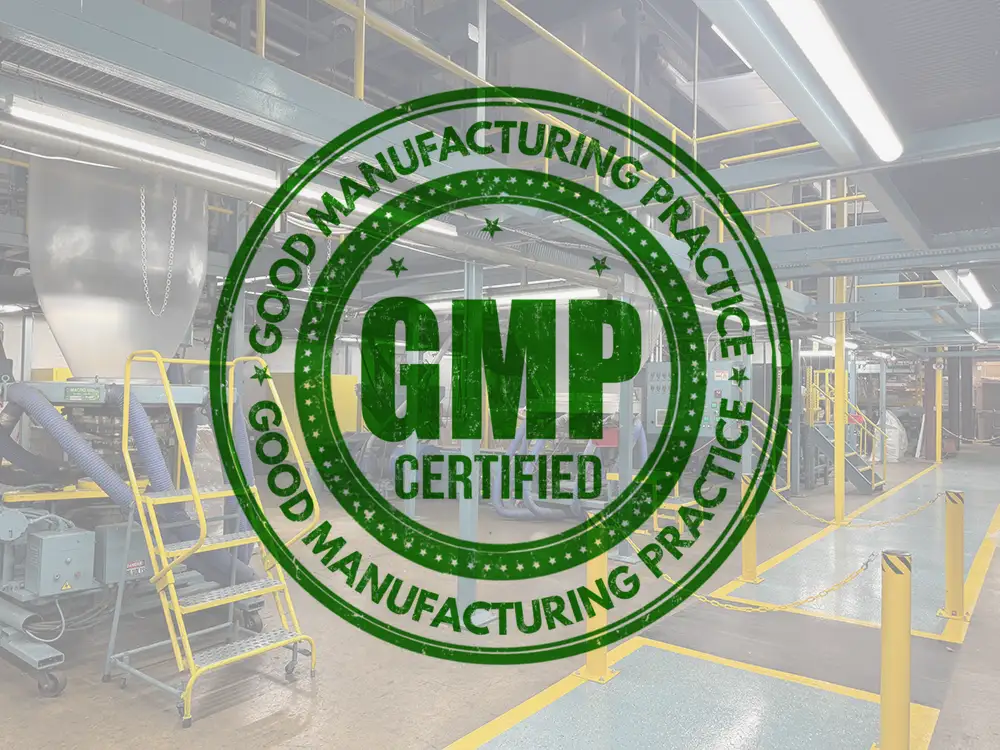
What is GMP?
GMP is an acronym that stands for Good Manufacturing Practices and is a set of standards and requirements set by the FDA created under the Current Good Manufacturing Practices guidelines. This acronym establishes the operational conditions and requirements that are necessary to ensure hygiene throughout the food chain and the subsequent production. GMP consists of guidelines that define management and handling actions with the sole purpose of ensuring favorable conditions for the production of safe food. They are also useful for the design and operation of establishments and for the overall development of the processes and products that are related to food.
The main objective of GMP is customer protection and includes many basic operational conditions and procedures that are required to be met by the food company. Obtaining a GMP certification demonstrates a commitment to both compliance regulations and to a high standard of quality control. A GMP audit is required by many retailers and can help you get your product into many stores. GMP certification requires you to have a HACCP plan (HACCP Certified Products, Food Bags, Packaging Supplies) as well, which is also an area we specialize in. When you turn to Dana Poly, you will be getting plastics that are GMP compliant. Ensuring GMP certified food packaging is delivered.
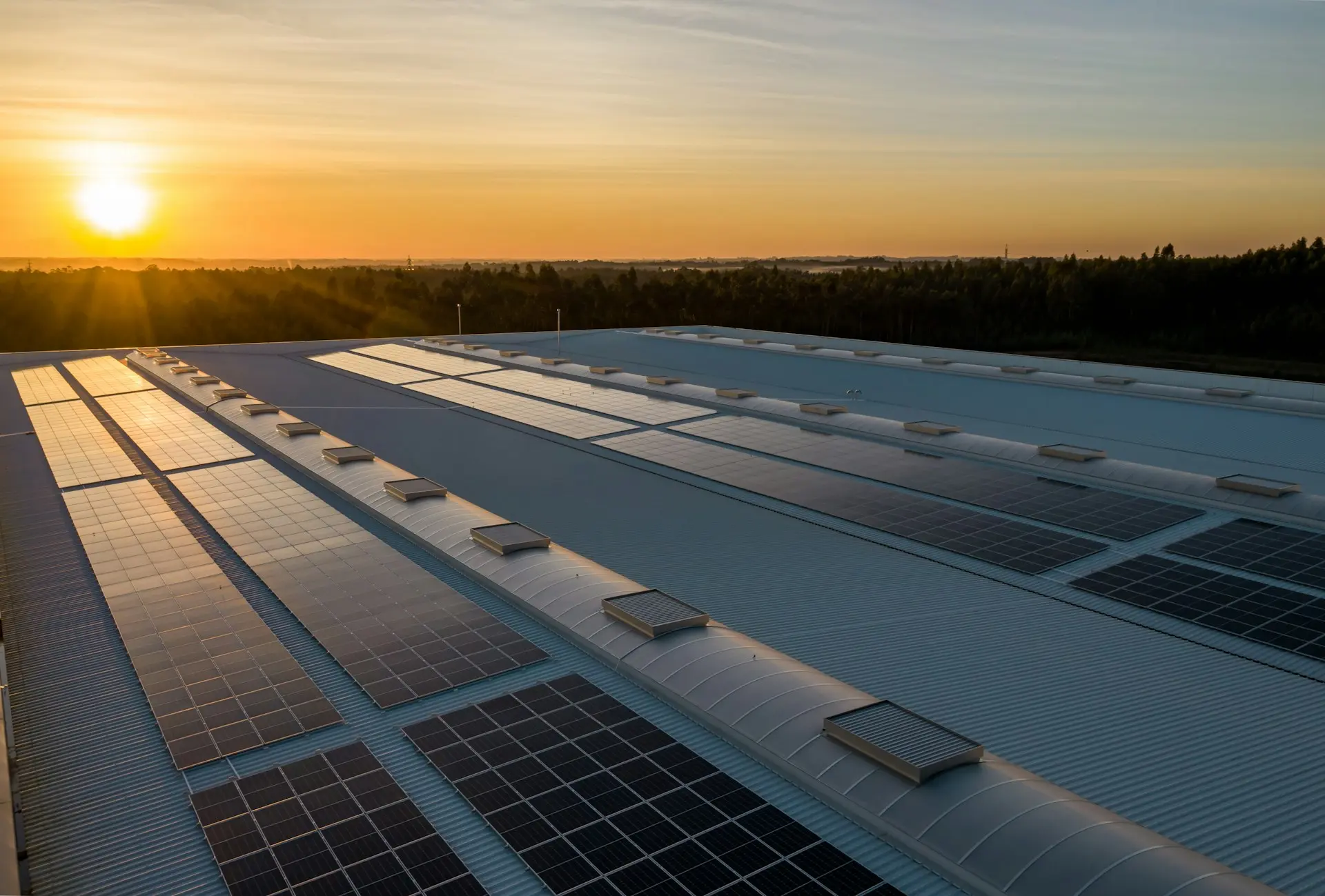
Common Examples of GMP Guidelines
Here are some common examples of GMP guidelines. During our manufacturing process, we make sure all of the plastic we produce is GMP certified for safe food packaging.
- training provided to employees.
- adequate maintenance of all equipment.
- construction and layout of food premises.
- cleanliness of premises, equipment, floods, walls, etc.
- implementation and effectiveness of the traceability system.
- identification and storage of waste within and by the company.
- use of suitable chemicals within and around the food premises, including cleaning chemicals, machine lubricants, and pest control chemicals.
These are all common examples of GMP guidelines. When you turn to Dana Poly for GMP compliant food packaging, we deliver. Ensuring you stay GMP compliant.
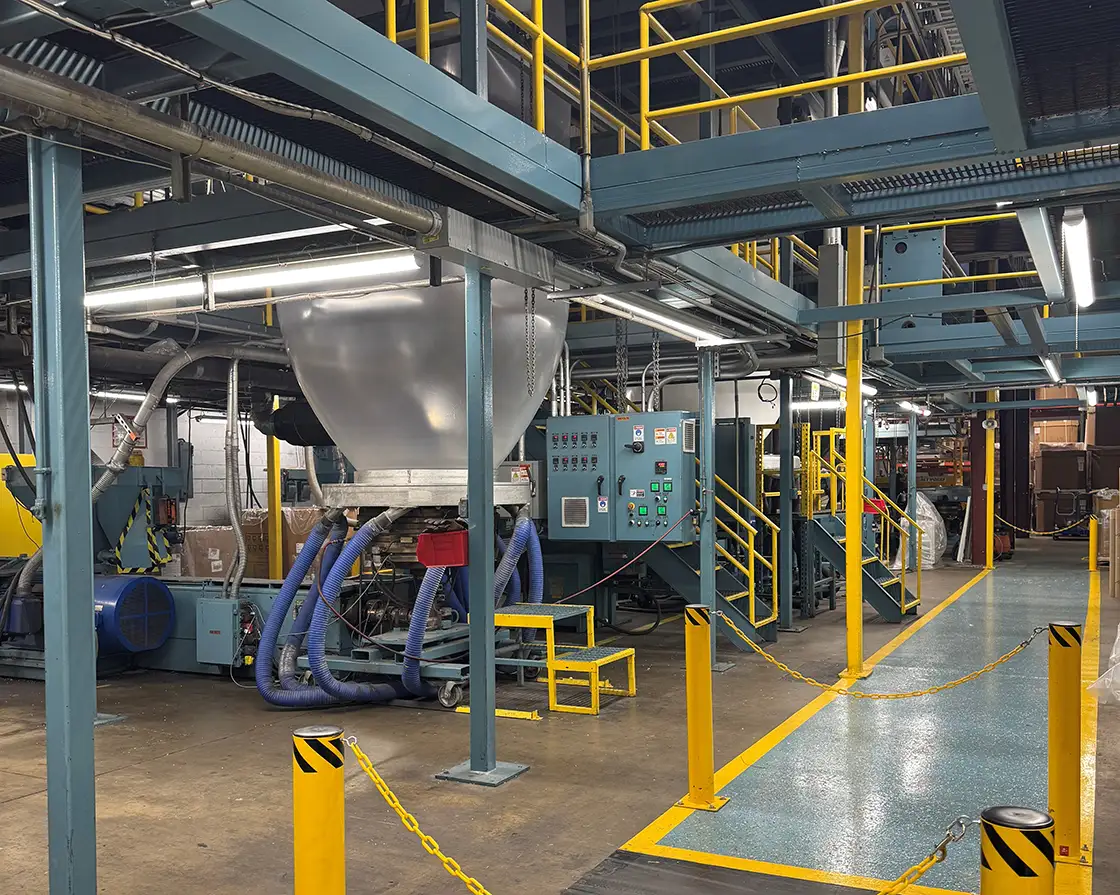
What GMP Compliance Helps With
Here are some common ways you are helped when you are GMP compliant.
- clear evidence of safe and efficient food handling
- compliance with all legal requirements
- builds trust with customers
- reduces costs
- saves resources
- provides food culture within your company
- offers the ability to trade around the world with other GMP compliant buyers
- reduction of returns, reprocesses, rejections and claims
By following these Good Manufacturing Practices, we are ensuring that every client with deal with is compliant in this aspect.
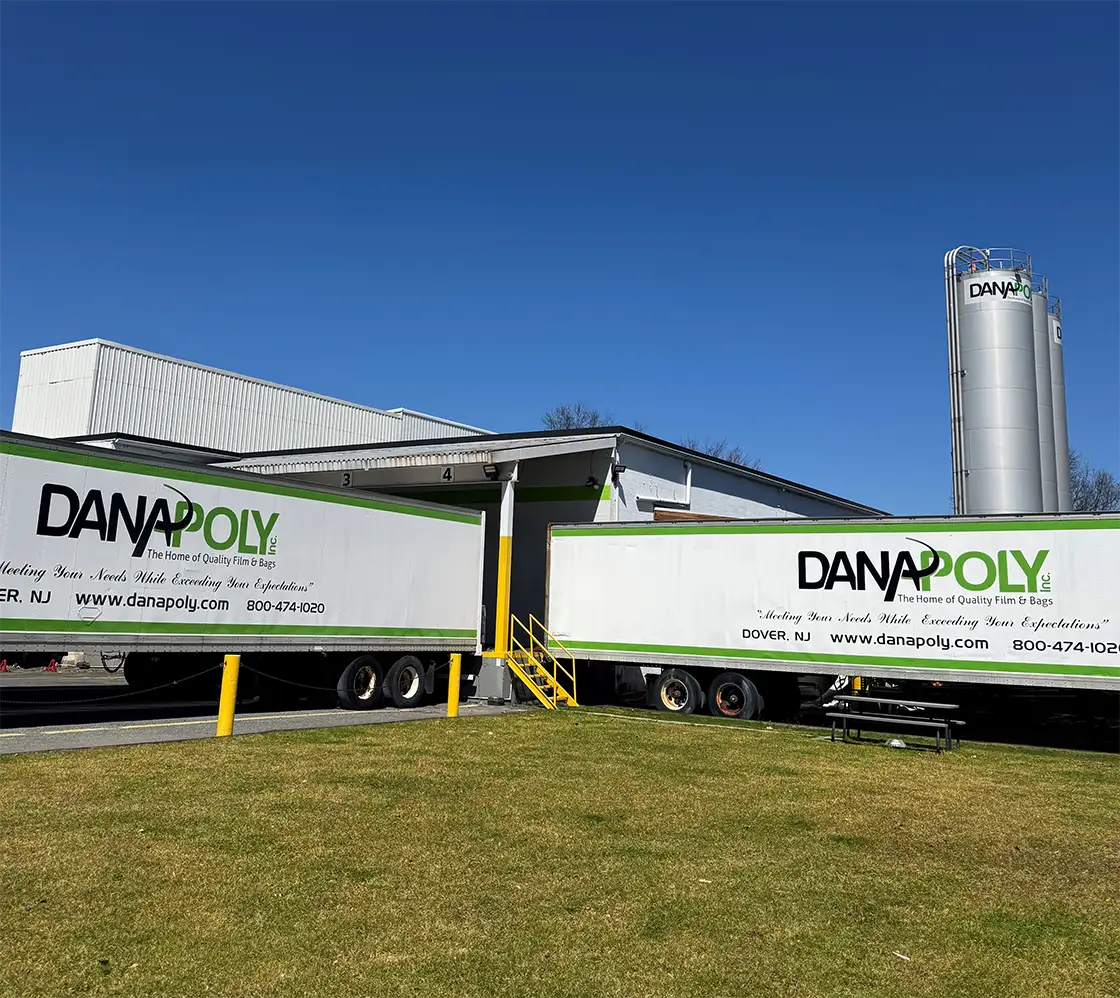
Requirements of a GMP Certification
Employees
Employees must not be sick while working. They must also follow hygiene practices so as not to contaminate products.
Facility Requirements
The plant and grounds must be in sanitary working order according to specifications and the plumbing must be in sanitary and working order according to CGMP guidelines.
Sanitary Operations
Only the use of safe non-toxic cleaning chemicals around production is permitted. Toxic chemicals are only allowed if absolutely necessary in the cleaning of equipment or other instances where only that specific chemical can be used. All toxic chemicals must be stored away in a secure manner.
Also, pest control is a must for all facilities. Pesticides can only be used when it will not result in contamination of any sort.
Processes and Controls
All parts of the processing operation must have proper sanitation before, during and after use. Trained employees must be responsible for proper cleaning of the equipment. In order to ensure there has been full sanitization, testing is required, such as swabs sent to labs
Manufacturing Operations
Equipment and utensils are to be kept clean and maintained. On top of that, they must be used and constructed in a way to not contaminate products. The packaging and filling and assembling processes must not introduce any contaminates.
Defect Action Levels
Consistent quality control must be employed at all times in order to detect any defects.
Equipment and Utensils
Equipment and utensils must be cleanable and in clean conditions. They cannot shed metal fragments or lubricants during use.
Warehousing and Distribution
Storage buildings and distribution vehicles must protect the products from any potential contaminants.
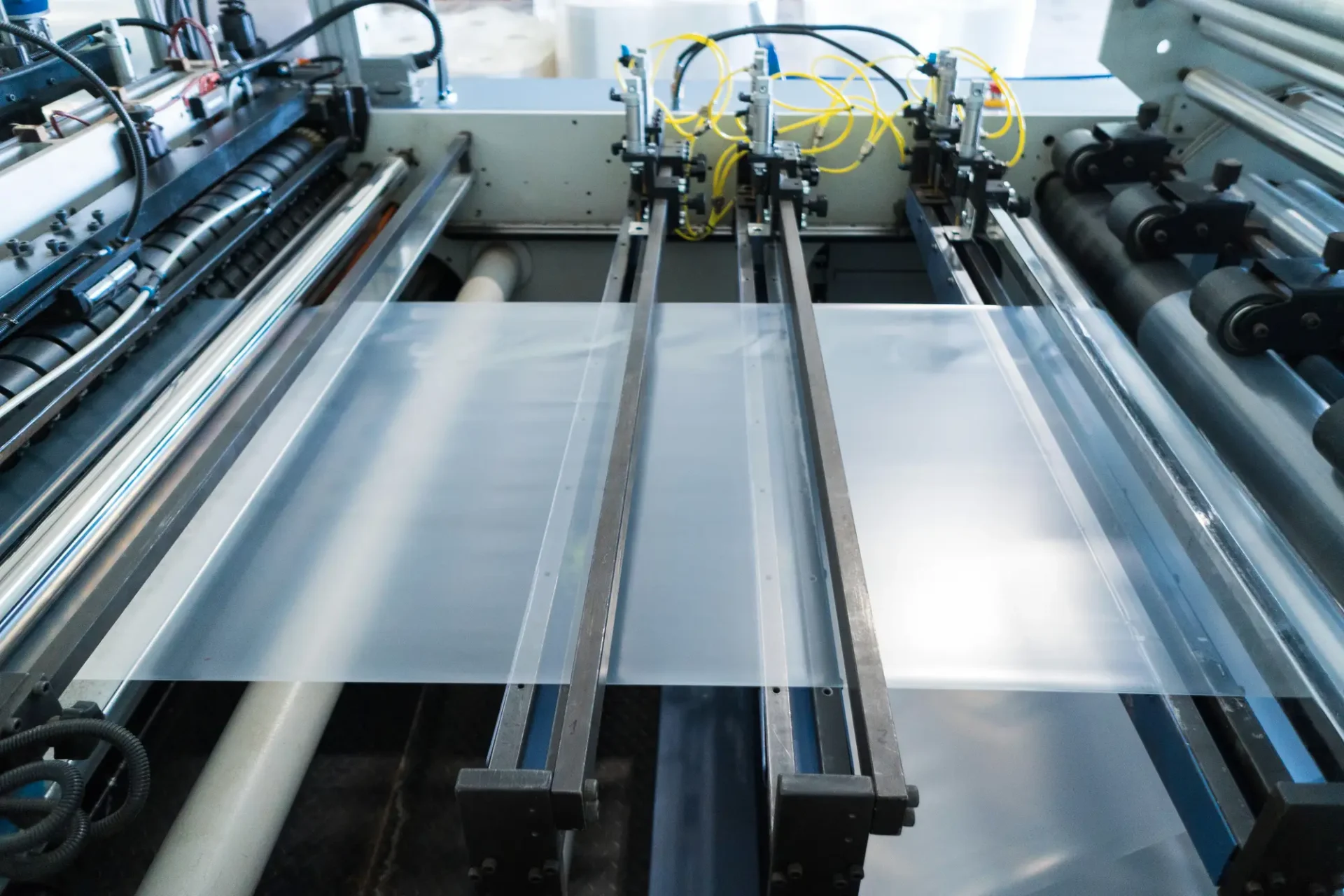